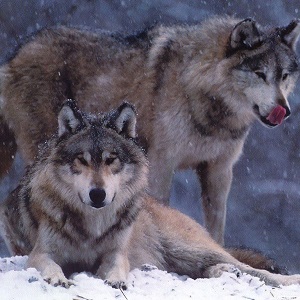
Inspired by Nature
All our designs are inspired by nature, Native American legend, and life. Animal spirits are all around us and, according to legend, visit us, accompany us, and guide us in our every day lives and decisions. In legend and stories passed around tribal fires, ancestors often took on the trappings of animals in order to harbor their spirits. The wolf is sharply intelligent with strong instincts.
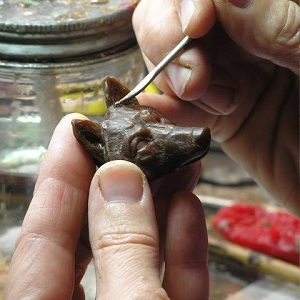
Artistry in Wax
"...I use Victory Brown sculptor's wax, which is a microcrystalline wax, to carve my originals. It is an extremely plastic wax, soft and smeary, but it yields results that can’t be achieved with any other wax! I really like the fact that I can leave my fingerprints at the outer edges, and I can push and pull this wax like clay."
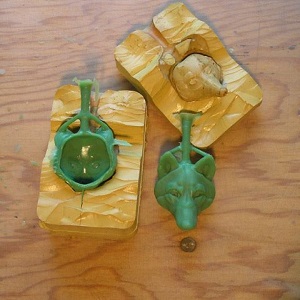
Lost Wax Casting
The wax or waxes are sprued and fused onto a rubber base, called a "sprue base". Then a metal flask, which resembles a short length of steel pipe that ranges roughly from 1.5 to six inches tall and wide, is put over the sprue base and the waxes. Most sprue bases have a circular rim which grips the standard-sized flask, holding it in place. Investment (refractory plaster) is mixed and poured into the flask, filling it. It hardens, then is burned out as outlined above. Casting is usually done straight from the kiln either by centrifugal casting or vacuum casting.
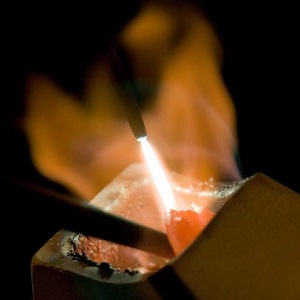
Molten Metal
Molten metal is quickly poured into the disposable mold either under vaccuum or with the help of a centrifugal casting machine. The metal melts at temperatures from 850-1000 degrees C and must be free from impurities and oxidation. We work with Bronze, Sterling Silver, and various purities and colors of Gold, each with their own unique challenges and peculiarities when it comes to casting.
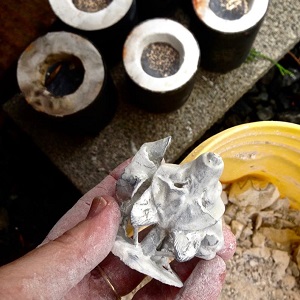
Castings
The finished castings are perfect! All that is left is hours of attention in detailing, polishing, and applying finishes that can include sandblasting, plating, and stone setting. These castings are in sterling silver, but could also be done with bronze, or even yellow or white gold. While the techniques are the same, the melting temperature is slightly different and the unique character of each metal makes the process individual for every piece. Plus, the cost of raw materials varies greatly with gold at the top of the chart!
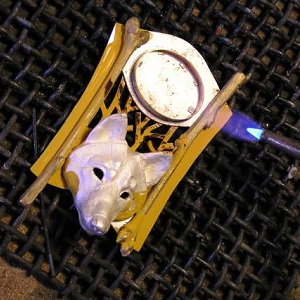
Assembly
The raw castings provide the base for the design which requires intensive hand assembly and attention to detail. While the simplest designs have minimal assembly work required, most designs have at least some soldering, hand finishes, and even stone setting. This wolf will take a bit of everything to complete with multiple metals and several different stones to set and interesting finishes to apply!
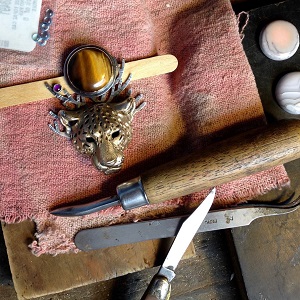
Stone Setting
Setting a stone. Tools used to tighten a bezel around the edge of a cabochon: an Old Timer knife, a bezel pusher made from an old file, and a burnisher. I use a popsicle stick to support the stone while pressing down. These types of gemstones are durable but can be fragile under the pressure required to properly secure into the bezel settings. I take my time and apply only enough pressure to feel the metal begin to move under my bezel pusher or burnisher.
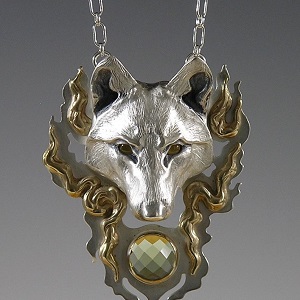
Fire Wolf
The wolf is one of the most iconic spirit animals, indicating intelligence and strong instincts. This Fire Wolf is accented with 14K and set with a checkerboard lemon quartz.